Production Module - BOM and Routing
Bill of Material (BOM) is a base functionality of setting up production module of an ERP system. A manufactured item consists of components, which are used to build the product through production operation(s). The main use of BOM is to define product structure of a manufactured end item.
Routing is another important base of production module, which defines the method of manufacturing. Method or route to be followed for manufacturing a product is a prerequisite for setting up production module.
Bill of Materials: Any manufacturing process goes through various phases of production and at each phase, components (either work in progress or purchased) are needed. BOM details components required at various phases or levels of operations (either single level or multi level). In a multi level BOM, a parent/child relationship between successive levels is formed.
BOM is used both for production and planning purpose, as specified below:
- Defining a production bill of materials: The end item is described at highest level of BOM. Levels of BOM are defined indicating material-routing relationship at every level of operation. Thereafter, components are added at each level. An existing BOM can be easily modified to create a newer version of BOM. An Engineering Bill of Material from Engineering Data Management module may also be copied to make a production BOM. A generic BOM may also be modified to make a customized product with the help of Configuration Management module.
- Defining a planning bill of materials: Production of similar items (such as garments of same type but of different sizes) is linked through aggregate relationship under planning bill of material so that their long term plan of production/ subcontracting are not done separately.
Loops in BOM - While defining multi-level production bills of material, the user may mistakenly link a higher level item to its component at a lower level. This creates a data error and triggers an infinite loop for the manufactured item. This mistake is detected through utilities, which normally forms part of the module.
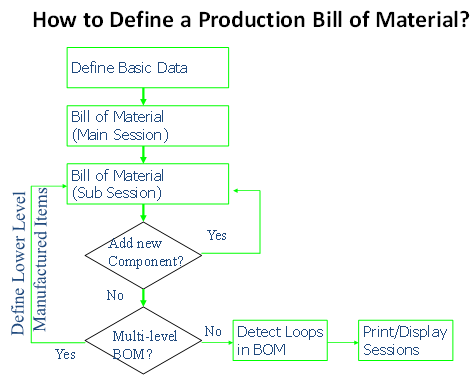
Routing - The objectives of Routing module are:
- All tasks required to manufacture an item are determined.
- The work centers related to these tasks are identified.
- The sequence of task linked operations to be carried out on work centers or sub contracting work centers are established.
Department - An organizational unit that carries out a specific set of tasks. A department can be of various types such as work centre, service centre, sales office etc.
Work Centre - A Work Center is a place where production activities are performed. Resources (like men and/or machines) are linked to a work centre. Thus, a Work center is a group of resource units used as a functional planning unit. . Work centers may be departmental work centre or sub contracting work center.
Task - This term is used to describe any activity carried out on the shop floor. Work centers and machines (for machine tasks) are used to define tasks. Task may be of various types such as production, repair etc.
Work centre Task relationship - The task is linked to the work center if the work center is able to executing the task. Details such as set up time, production rate etc. are maintained under this relationship.
Routing Code - The routing code identifies a routing sheet. Multiple (alternative) routings are possible for each standard manufactured item. A routing selection can depend on the order quantity, which is called the Order Quantity Dependent Routing. A routing code is needed to be linked to the manufactured item.
Routing Operation - Here, series of routing steps that are carried out successively to produce an item is defined. The operations are identified by serial number, which indicates sequence of operations for the associated manufacturing process.
The main flow between business objects in Routing module is depicted below
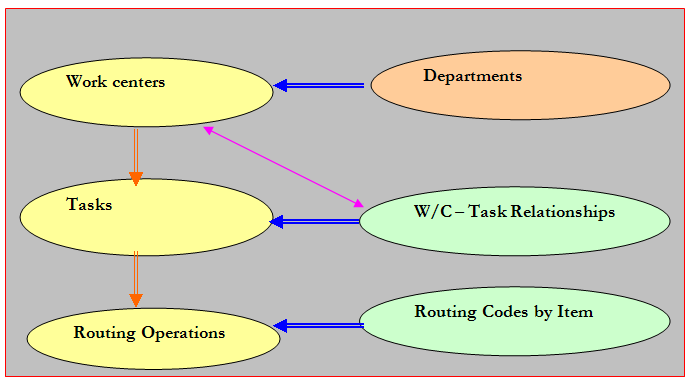
❮❮ Previous | Next ❯❯ |
Related Articles
- Asset Management & Budgetary Control
- Cost Estimate and Accounting
- Cash Management Module in ERP
- Production Planning and Control
- Subcontracting and Materials Issue
Authorship/Referencing - About the Author(s)
![]()
The article is Written and Reviewed by Management Study Guide Content Team. MSG Content Team comprises experienced Faculty Member, Professionals and Subject Matter Experts. We are a ISO 2001:2015 Certified Education Provider. To Know more, click on About Us. The use of this material is free for learning and education purpose. Please reference authorship of content used, including link(s) to ManagementStudyGuide.com and the content page url.